Keeping workers safe starts with knowing which gloves your workplace really needs
The Workers’ Compensation Board of Canada says that there are at least 250,000 lost-time injuries in Canada every year, and almost 23% of those are hand- or finger-related. In other words, more than 50,000 Canadian workers are injuring their hands every year.
Fortunately, hand protection technology has come a long way in the past few years, and it’s easier than ever for employers to ensure their workers stay safer when on the job. But how do you know which gloves to choose for your team?
ANSI cut resistance standard
The benchmark for choosing the right gloves for the right job starts with the ANSI Cut Standard. This measures cut resistance for industrial work gloves on a scale of A1 (low cut hazards) to A9 (extreme cut hazards). Matching the job to the scale ensures you know which type of glove you need.
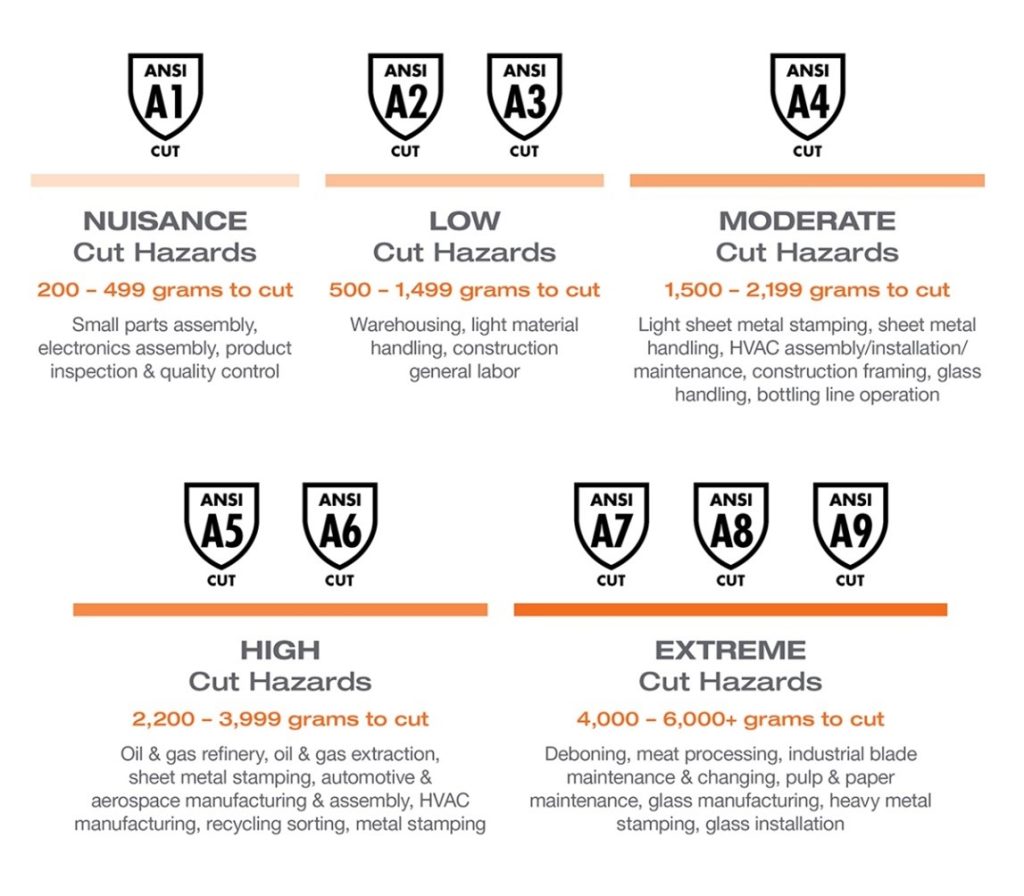
How to assess your needs
The best way to ensure you’re providing the right gloves for your workers starts with an assessment.
- Document all the tasks your employees are doing in a given day. Whether they’re just going to be out in the cold, or handling sharp blades, you’ll need to know their risk levels.
- Make a list of potential hazards. This could be understanding the chemicals and equipment they’re using, or the types of materials that might cause cuts and punctures. Don’t forget to include hazardous liquids.
- Consider what injuries may have happened in the past. Whether you’ve had a history of punctures, burns or other injuries, this can give you a good indication of what you most need to protect against.
- Consider fit. Gloves work best when they fit properly, and not all your employees have the same sized hands. You’ll want to ensure you have the right sizes for the job.
- Undertake a TCA (Total Cost Assessment). It doesn’t make sense to buy ‘cheap’ gloves if they wear out faster than higher-quality ones – especially when poor gloves can mean reduced wear time, decreased productivity and increased costs overall.
Talk to a glove expert.
Your employees are performing hundreds and thousands of tasks with their hands every day. And there are hundreds of different kinds of gloves on the market. If you’re having trouble figuring out which ones make the most sense for your organization, why not ask us? We’re not affiliated with one particular glove manufacturer, and most of our team has been working in the safety equipment field for 20+ years – so we know what works.